Interviewing a MODG Student ‘Knifesmith’
Hello all! I have had the privilege to be able to speak with high-school junior Liam Martin, one of Mother of Divine Grace School’s very own, and learn more about the somewhat unique extracurricular activity he enjoys outside of school. This student happens to be an aspiring and talented amateur knifesmith, and he has kindly agreed to allow me and you a glimpse into his knifesmithing life. So here goes!
When was it that you first became interested in crafting knives and what was it that initially inspired you?
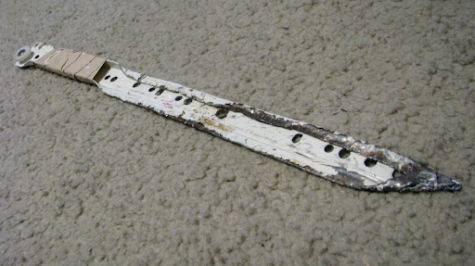
“Let’s see. So, I made my first knife I think in 2019, sometime in the summer, July I believe. I had been cleaning out the garage, and I happened upon a small rail from a disassembled Ikea drawer set. The inspiration came from the end of the rail, with the small wheel. To me, it looked like the perfect handle. So I hammered the other end flat, pointed the end, and wrapped the handle in tape. It was a prison shank, in a frank manner of speaking. It was ugly, that much I will admit. But that is my start. I have always been interested in weaponry, whether bladed, blunt or bullet, I have always been fascinated by them. So to make them for myself was an inspiration I could not pass up.”
How would you describe your workspace? Are there limitations to working within the confines of your home that have led you to act differently than you might in a professional workshop?
“My workspace? Let’s say limited and also organized in a strategic-convenient fashion.
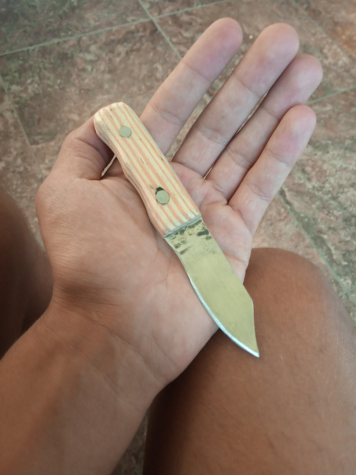
“It’s basically a wreck. I use the term strategic-convenient because why put something away that I am going to need ten minutes later? Or put away the file that I will need 27 times and have to get it back out again? Instead, I have everything I need already out and when I am finished I will clean up. It has been pretty clean, believe it or not. As for limitations, there are a lot. I can’t use any power tools past 8:30 is one. I also don’t have very great safety features. Typically, you don’t want to grind metal and sand wood in the same area, because the hot sparks from cutting metal can ignite sawdust, but I have no such space for safety measures like that. I do put up some steel diamond plate to protect stuff from the angle grinder’s spark shower. But that’s kind of it. If I had a professional shop, then I would separate wood and metalworking areas, and I would also have the chance to spread out some of my machinery. But working in this small corner has given me great insight into the value of space management and making do with what you have.”
How has your work progressed over the years? Obviously you have become more skilled, but have you begun to incorporate new styles into the knives you make or new techniques into the actual knife making-process?
“My word, yes. If you look at the difference between my first and my latest knife, then you will understand. I have incorporated a lot of new techniques into my craft and some new styles yeah. For starters, I have been using bevels. So, a knife starts as a plank of steel, and the bevels give it that triangle profile. (See example in picture slide at the top of this article.)
“So the angled-down sections of the blade are made by running the steel at an angle across a grinding surface. This was a technique I dabbled in, but lately have been getting much more serious with.
“Another technique is doing a full tang. So, a full tang is where the blade and handle are one piece of steel. So a full tang, like this, has two pieces of wood or other material for the handle on either side of the tang. Tang is the name for the section of the blade that extends into the handle. (See example in picture slide)
“Some other techniques are finishing. For example, using toothpaste to polish the blade. Toothpaste has a grit equivalent of 600 grit, so pretty fine and smooth. I also oiled the handle of my last knife to give it protection and to make sure it didn’t dry out and crack. I also waxed it with some homemade handle wax to seal it all up. In general, making it look more like a knife and less like a prison shank.”
Do you have a knife which you are particularly proud of, and if so, why?
“Yes, for sure. My latest knife was by far and away the best I have ever created. It looked artistic, almost. Like it held my personal touch and style in it. It was definitely mine in a sense. It felt like a proper knife is all.”
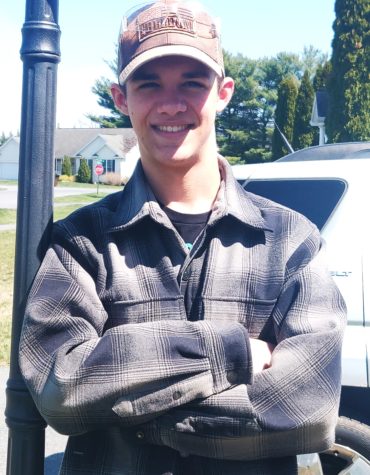
How do you plan to proceed with this talent of yours into the future? Do you plan on ever using this gift of yours as a career?
“Make more knives! Branch out some, try new things. I have a mop handle and a squeegee handle that I want to turn into a scythe of some sort. Make some swords, who knows? I am not sure about a career, but likely a side-hustle. I might start selling this summer. I already have three buyers lined up, but no time to work on their knives. One customer is my dad’s friend who is buying two. I am quite excited to get those finished.”
How would you say that you are able to use this God-given gift of yours to bring God the greater glory?
“That is way too philosophic for a dumb grinder jockey like me. Not sure how I could tie knife making into giving God glory, but there is probably a way. A wise man once told me that developing and perfecting your God-given gifts and talents is a way to give God glory, so I guess that is one way.”
And that is all for now! If you yourself are a talented MODGer who would be interested in sharing your abilities with us, reach out – we would love to talk with you!
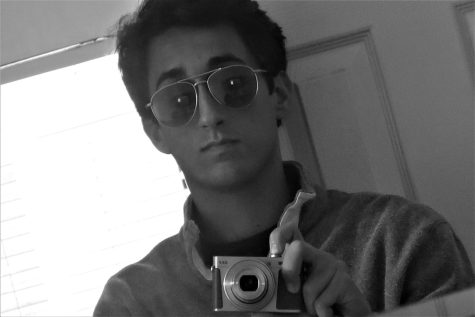
Among other things, JohnPaul Pascale dabbles in writing (especially politically motivated), thoroughly savors a good conversation, is always searching...
Ethan Priselac • Apr 20, 2023 at 4:21 pm
Great interview! Could you consider writing another with me, as I am a custom knifemaker with nearly four years of experience? I have made around a dozen or so knives and I pursue, not the art, but the practical useage of it.
JohnPaul Pascale • May 11, 2023 at 9:40 am
Ethan, I apologize for not responding sooner, I just saw this. I would certainly consider doing so! As you know, the end of the year is approaching, and the deadline for all news production articles is actually very early – May 16th. However, if you want to reach out to me, I can talk to you about the possibility of writing an interview with you over this summer and having it published this fall.
Corinne Oncena • Apr 15, 2023 at 9:41 am
This is a wonderful interview! I now know many things about knife making that I didn’t know before. Thank you for writing this!
anna • Apr 15, 2023 at 5:33 am
Loved this article! It was very informative and interesting, great job John Paul! And thanks Liam for sharing your passion with us!